Spoke shaves
I attended a class on building a spoke shave (taught by John Gunterman) and
got hooked. They are nice projects that don’t require much time, materials and
even skill. Because of this I find myself making them more and more. The main
drawback is paying $30 per blade. Since I’ve had good success making the blades
for most of my plane projects I started making spokeshave blades as well. Here
is a sampling of some of the shaves I’ve made (the one at the top is an antique
Sheffield that I used as my model). The shave below it is the first one I ever
made (done during the class). It is made of some nicely figured curly maple. The
shave below it is a scaled down version made of Kingswood. Its size it just
right for smaller scale work.
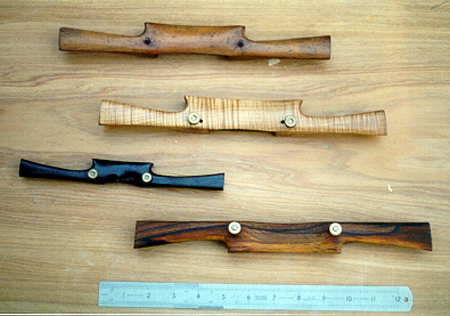
Round Shave
Used for working tight inside curves this spoke shave has a
rounded sole in front of the cutting iron. The wood used in its construction is
cocobolo.

Low Angle Shave
Original shaves were "low angle" designs. When manufacturers
began to mass produce them using cast iron for the construction of the bodies
(rather than wood which was the traditional material) the cutting geometry
changed to a "high angle" design similar to a bench plane. Stanley Tools Co.
developed a shave that utilized the original low angle geometry of the original
shaves (known as the "Razor Edge" spoke shave due to the resemblance between its
cutting iron and a straight razor). These "Razor Edge" shaves were very
effective but unfortunately finding an original in working order that is
affordable is becoming quite difficult! A couple of years ago Veritas (Lee
Valley Tools –
http://www.leevalley.com/wood/ ) developed their version of the "Razor Edge"
shave. It’s a great working tool unfortunately it utilized an aluminum body
(which works just fine but is rather ugly looking in my opinion). I purchased
one and made a new body for it in cocobolo. It didn’t improve it’s already great
performance it just made it look better! (Hey! It’s not good enough that your
tools work great, they must LOOK great too!)

Cabinet Scrapers
Similar in looks to a spoke shave a cabinet scraper has a thin
blade mounted almost vertically to produce a scraping action rather than the
typical cutting action of a shave. They are used for much finer work where only
a small amount of material can be removed (but they can be set to "hog" off
shavings at a surprising rate!). Because they scrape rather than cut they are
more suited to harder wood and are particularly effective at working difficult,
gnarly grain. Of all the different styles of cabinet scrapers my favorite is the
"Ram’s Horn" style. Not only does it look good but it’s a very comfortable
(ergonomic) style to use. The curved "horns" fit right in the palms of your
hands.
Scraper #1
This is a more delicate design used for finer tasks, especially
curved work. I made the "shoe" (the brass block that holds the blade in place
and creates the mouth) with a particularly fine mouth opening. The body is made
of cocobolo.
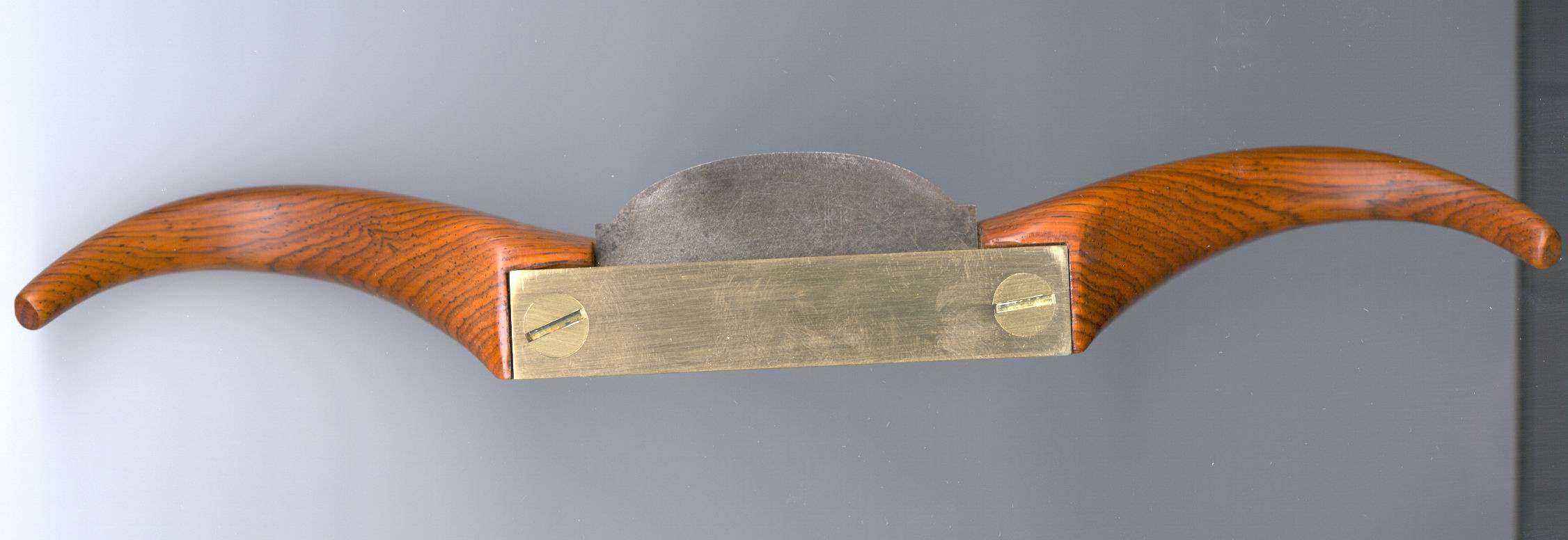
Scraper #2
This scraper is a much more "robust" version, capable of
removing quite a bit of material quickly or thin, wispy translucent shavings.
This shave was built using an old antique manufactured Ram’s horn scraper as its
model. I used the original cast iron shoe and blade. The original was most
likely made by Atkins but many manufacturers’ offered similar tools. This style
of shave was the predecessor to the Stanley #80 (which, of course is all cast
iron). I made the body of this shave from a piece of nicely figured Persimmon
(this wood was once very popular for the construction of golf club drivers
because it is so tough and split resistant). Since the piece of Persimmon I had
was not quite thick enough I added a sole of Ebony (which Persimmon is very
closely related to – often referred to as "American Ebony") which was attached
with a sliding dovetail joint.
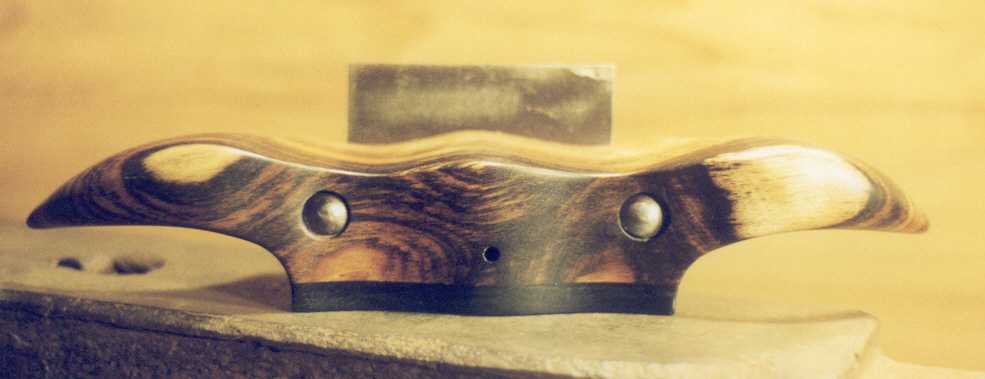
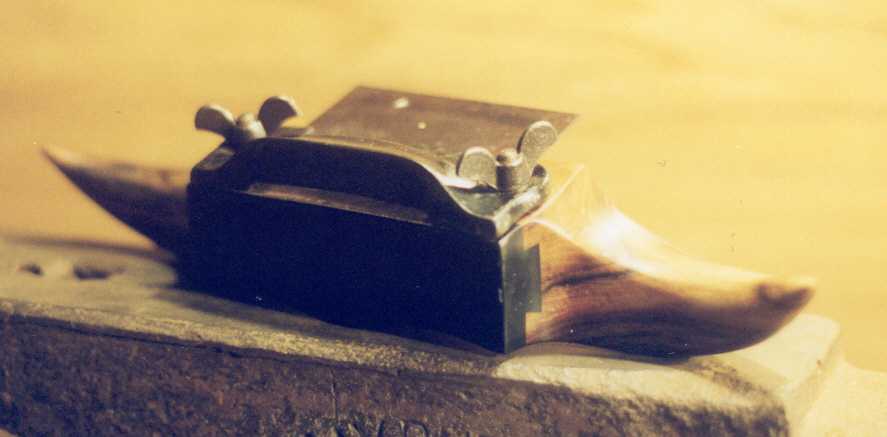
The original had a piece of stiff leather inlet into the area
just above the sole and behind the blade. This was used to force the blade into
a slight bend which helps the scraper cut more aggressively. Since this
arrangement only allows for a set level of aggressiveness I chose to solve the
problem of blade adjustment a bit differently. Borrowing from the design used on
the Stanley #80 that used a thumb screw to adjust the curvature of the blade I
bored and tapped for an Allen screw. You will notice the small hole located
opposite the blade just up from the sole. To adjust the blade curvature
(aggressiveness of cut) you simply insert an Allen key into the hole and turn
the screw. Works like a charm!
Gunstock
Scraper
Here's a "quickie" project I did a few weeks ago (I needed a
break from plane building so I
thought a few hours spent on something from start to finish was in order). It's
what I call a "Gunstock" scraper.
Last year I picked up an old model that was well beyond usability. The hickory
body was badly cracked and not worth fixing. You can see it just in the
background. Really got it more to use as a model and to perhaps salvage parts
from (but the only thing useable on this one was the metal toe piece - and it
was pretty marginal).
I made mine from some nicely figured Kingswood (the figuring is completely lost
in the picture). The only thing I was able to use from the original was the toe,
but it's mouth is a bit wide. I've since made another one from brass using the
same general dimensions and design. It has a much tighter mouth.
This small scraper (the body is a mere 7/16" X ½" in cross section!) is really
useful for shaping handles and such when I make hand saw handle or ones for bow
saws (even plane totes!).
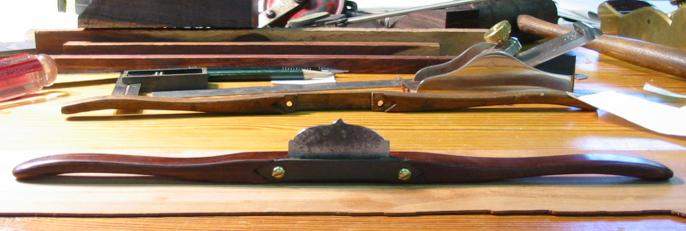